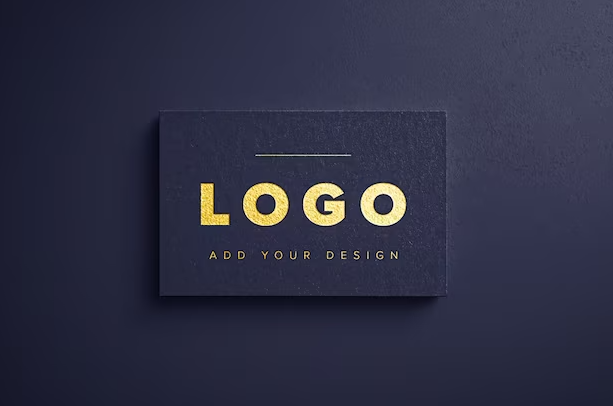
Hot stamping is a popular technique used in the printing industry to add luxurious and visually appealing designs to various materials, including paper packaging. The temperature used during the hot stamping process plays a crucial role in determining the quality of the final result. In this article, we will explore the effects of temperature on hot stamping quality and provide valuable insights for achieving excellent results in paper packaging.
Understanding Hot Foil Stamping
Before delving into the impact of temperature, let’s have a brief overview of hot foil stamping. Also known as hot stamping or foil printing, this specialized printing process involves the application of heat, pressure, metal dies, and foil film to create stunning designs on different paper types. Foil film comes in rolls with a wide range of colors, finishes, and optical effects, including metallic foils like gold, silver, copper, and holographic options.
Hot foil stamping serves multiple purposes in paper packaging. It elevates the packaging’s visual appeal, making it stand out from competitors. By incorporating a hot foil stamp of your logo or design, you can enhance brand recognition and customer awareness. The technique also ensures that your packaging catches the eye of potential customers when displayed on store shelves.
The Role of Temperature in Hot Foil Stamping
Temperature is a critical factor that significantly influences the quality of hot foil stamping in paper packaging. The correct temperature ensures optimal adhesion, sharp details, and vibrant colors, while improper temperature control can lead to various issues, such as incomplete stamping, blurred imprints, or adhesive problems.
Effects of Low Temperature
When the temperature during hot foil stamping is too low, the isolation layer and adhesive layer of the anodized aluminum foil fail to melt sufficiently. This results in incomplete stamping, blurry imprints, and overall poor quality. It is important to note that the hot stamping temperature should never be lower than the temperature resistance range of the anodized aluminum foil. The lower limit of this range ensures proper melting of the adhesive layer.
Effects of High Temperature
On the other hand, using excessively high temperatures during hot foil stamping can lead to different issues. When the hot-melt film melts beyond the acceptable range, it can cause the electrochemical aluminum to adhere around the imprint, resulting in a “paste plate” effect. Additionally, high temperatures can cause the oxidation and polymerization of synthetic resins and dyes in the electrochemical aluminum dyeing layer, leading to foaming or clouding in the imprints. Moreover, overheating can oxidize the surface of the anodized aluminum plating layer and dyed layer, resulting in a loss of metallic luster and reduced brightness in the finished hot foil stamped product.
Determining the Correct Hot Stamping Temperature
To achieve optimal hot foil stamping quality, several factors must be considered when determining the correct temperature. These factors include the model and performance of the anodized aluminum, stamping pressure, stamping speed, stamping area, structure of the stamping graphics, color and thickness of the ink layer of the printed matter, and the temperature of the hot stamping workshop.
The hot stamping temperature should be adjusted based on these factors. For example, when the stamping pressure is low, the machine speed is high, the base color ink layer of the printed matter is thick, or the workshop temperature is low, the hot stamping temperature should be appropriately increased. The general range of hot stamping temperature typically falls between 70℃ and 180℃.
It is crucial to maintain a consistent and constant hot stamping temperature throughout the process to ensure the stable quality of the products within a batch. However, it is important to note that different graphic structures on the same layout may require different hot stamping temperatures. In such cases, using different types of anodized aluminum at the same temperature or utilizing two electric heating plates and voltage regulating transformers can help achieve the desired results.
Quality Control Checks
In addition to temperature control, conducting quality control checks throughout the hot foil stamping process is crucial to ensure a high-quality end result. Quality control checks should include verifying foil coverage, adhesion, and color consistency. This helps identify any defects or issues that may impact the final hot foil stamped product and allows for adjustments or corrections to be made in real-time.
Conclusion
Temperature plays a vital role in determining the quality of hot foil stamping in paper packaging. Achieving optimal temperature control ensures proper melting of the adhesive layer, vibrant colors, sharp details, and excellent overall quality. While low temperatures can lead to incomplete stamping and blurred imprints, high temperatures can cause adhesive issues, foaming, clouding, and a loss of metallic luster. By carefully considering the various factors involved and conducting regular quality control checks, businesses can achieve outstanding hot foil stamping results in their paper packaging projects.