1.Designing the paper bags
The designing is the key process for customizing high-end paper bags,in order to produce upmarket paper bags matching client’s requirements,Hrenary packaging will use their brains in the post-printing surface decoration process, such as bronzing, UV, glazing, colorful, The flexible use of concave-convex and flocking processes
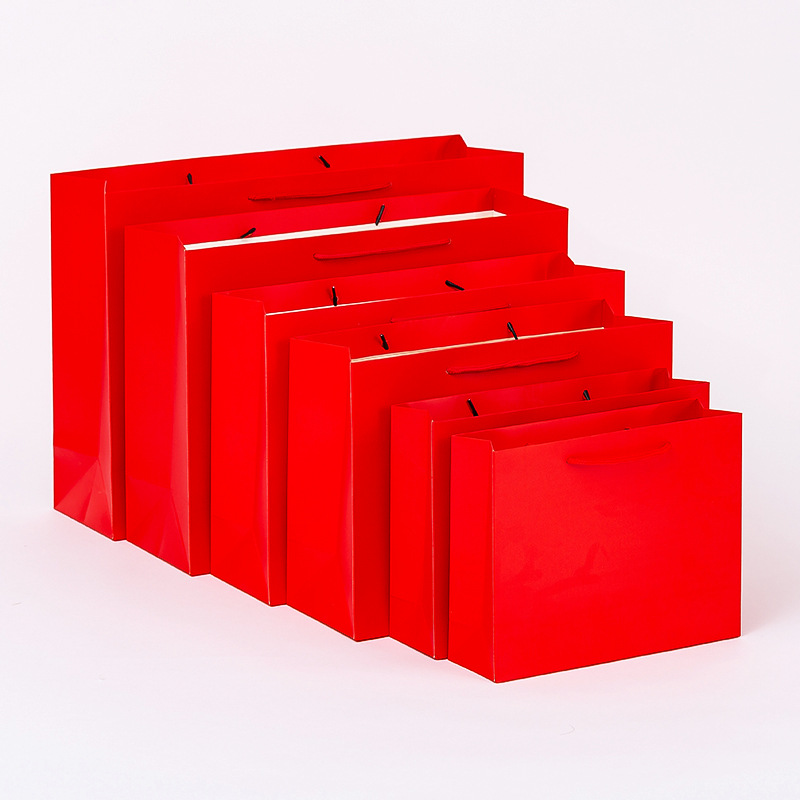
2.Choose reasonable paper material
Most of the paper selected for custom paper bags is selected from kraft paper, cardboard or coated paper, among which kraft paper has good toughness, high strength and rough surface. Cardboard has good stiffness but poor toughness, and generally requires surface coating when used as a paper bag. Coated paper has certain toughness and rich printing colors, but its stiffness is worse than cardboard. In the process of customizing paper bags,hrenary will choose suitable paper to customize according to the requirements of customers. For example, customers emphasize durability and choose kraft paper. When they are particular about color and stiffness, most of them use cardboard, and if they need rich and gorgeous pattern effects, they will choose coated paper.
3. Printing
Normally,we use CMYK/PMS colors to print on the personalized gift bags,Here highly recommend high-quality printing machine for printing. A good printing machine has a well-proportioned ink volume control and better color brightness.
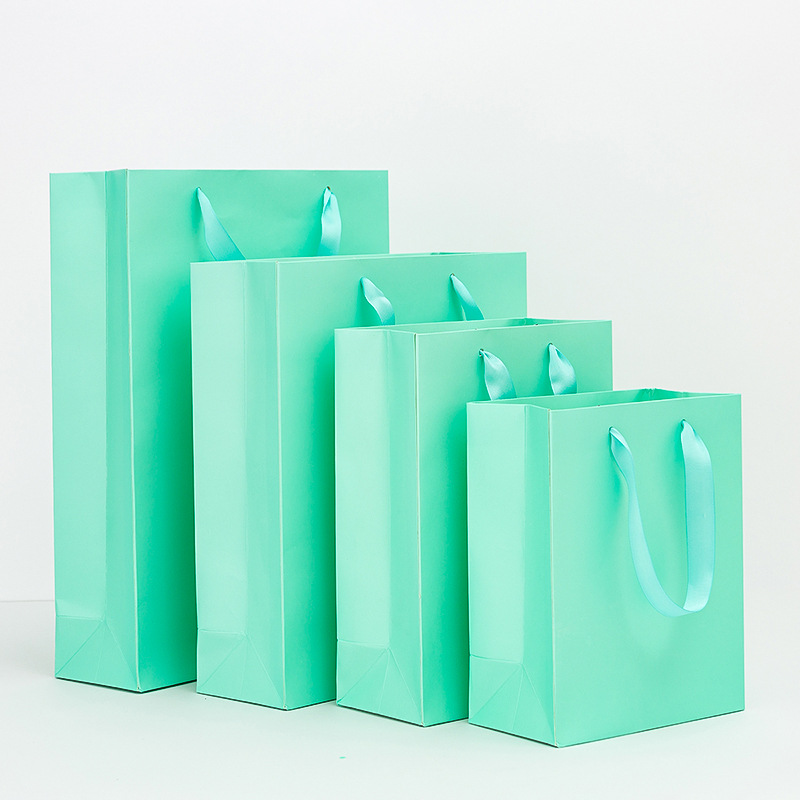
4. Lamination
Lamination, also known as post-press plastic, post-press lamination or post-press lamination, refers to covering a layer of 0.012-0.020mm thick transparent plastic film on the surface of the printed product to form a post-press finishing that integrates paper and plastic. The process is generally divided into two processes: pre-coating and instant coating. root
According to the different film materials used, there are high-gloss films and matt films.
5. Surface finishing
Hot stamping, UV, glazing and other printed product surface finishing processes are widely used production processes for paper bags. It greatly satisfies people’s pursuit of exquisite and high-grade paper bags. In the production process, Hrenary Packaging strictly controls the
key point.
6. Die cutting
The die-cutting process is a process of combining a die-cutting knife and an indentation knife on the same template and using a die-cutting machine to die-cut and indent the printed product, also known as “rolling”. It is an important process in the production process of paper bags. The quality of die cutting directly affects the quality of paper bag forming and the efficiency of manual pasting.
7. Gluing
Hrenary Packaging’s custom paper bags have always followed the combination of process mechanization and labor. The paste process is the most special part of the production of portable paper bags, which mainly relies on manual completion.Hrenary Packaging strengthens detailed control in the manual paste process to prevent spilled glue pollution and avoid scratches on the surface of paper bags during production.
The hand-pasted paper bags have basically been formed, and some paper bags have the final process – punching, threading and other operations, so as to complete the final packaging of the paper bags.
The design and production of paper bags is the key link of the whole paper bag production process. In order to improve the taste and grade of portable paper bags, the designers of hrenary Packaging will use their brains in the post-printing surface decoration process, such as bronzing, UV, glazing, colorful, The flexible use of concave-convex and flocking processes also makes the paper bag brighter in color, enhances the three-dimensional sense, and has more expressive power.
The above 7 points are basic process of customizing luxury shopping paper packaging,Hrenary packaging(www.hrenarypackaging.com) have 10+years experience in producing paper bags,more details,pls contact us.